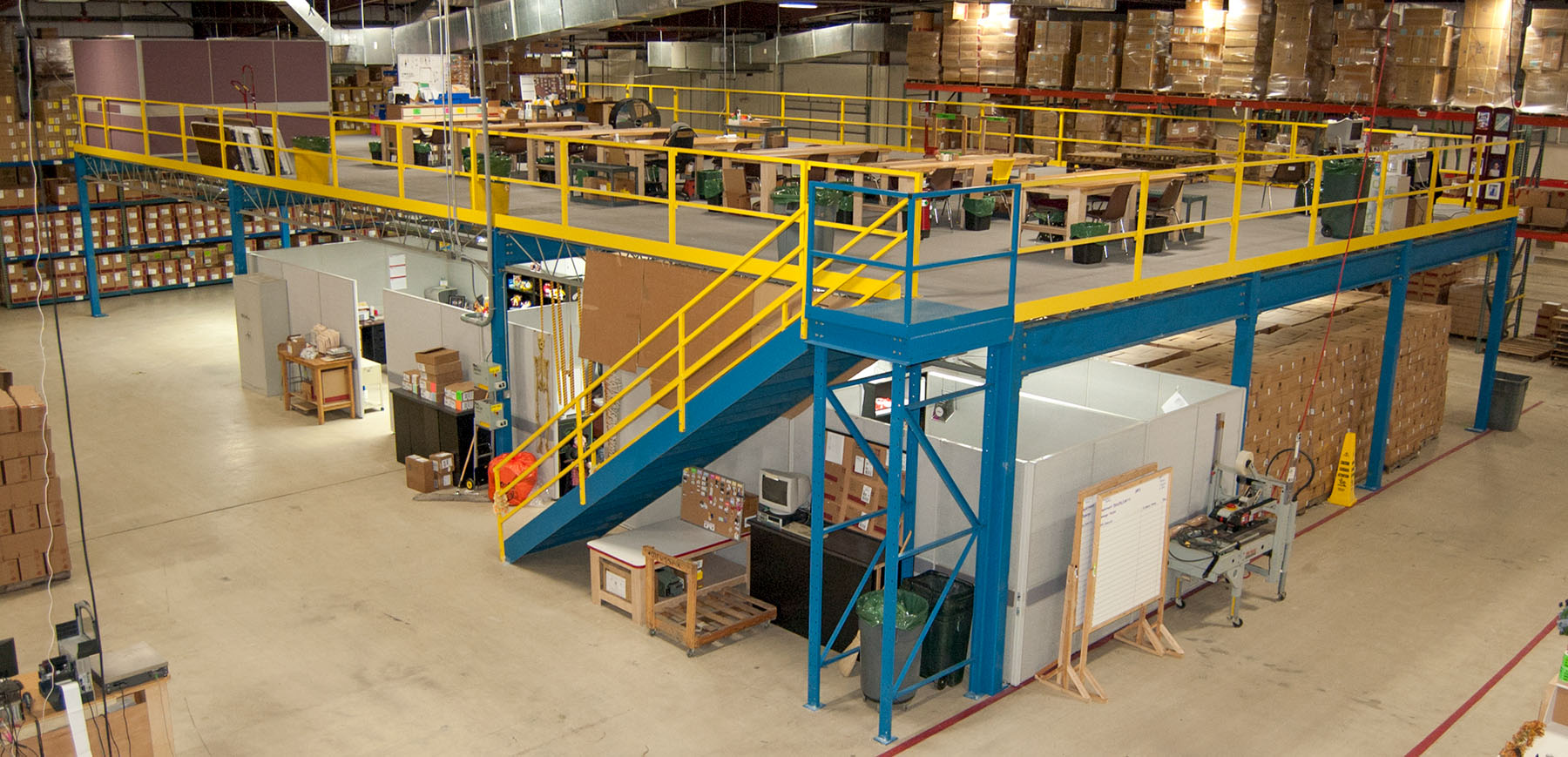
05/01/2024 0 Comments
How to Choose the Right Warehouse Racking System
A warehouse racking system, also known as a pallet racking system, is the backbone of any warehouse infrastructure. It involves metal upright frames and horizontal beams to hold pallets, cases, and oddly shaped merchandise securely. These systems typically range from 15 to 60 feet tall, often necessitating a forklift for material retrieval.
Choosing the right warehouse racking system is crucial for enhancing your warehouse’s efficiency, safety, and storage capacity. With numerous options available, finding the ideal system can feel daunting. Follow this guide to help simplify the selection process and ensure you make an informed decision that aligns with your warehouse’s needs.
Key Factors to Consider
Here’s what to think about as you narrow down the right rack system for your warehouse:
· Product and material flow: Consider how inventory moves through your warehouse. Different racking systems suit various inventory management methods, including first-in, first-out (FIFO) and last-in, first-out (LIFO).
· Warehouse layout: The layout, especially the vertical space available, impacts your ideal racking system height.
· Pallet characteristics: The size, shape, weight, and quantity of your inventory are crucial considerations. For example, the rack depth influences storage density, with options like double-deep or single-deep racks available.
· Budget constraints: While working within your budget is essential, investing in a more durable, higher-priced system may offer long-term benefits.
· Safety considerations: Choose a durable storage system suitable for the application to ensure employee safety and operational efficiency.
· Accessibility and versatility: Make sure the racking system is accessible to your existing material handling equipment and adaptable to the different product types you may be required to store.
Types of Racking Systems
With the above factors in mind, you’re ready to sift through your options. Here are the most popular choices:
· Selective racking is ideal for FIFO inventory, providing direct access to each pallet. This system comes in single- or double-deep configurations.
· Pallet flow racking is best for high-volume operations and FIFO systems, using gravity to move pallets along sloped lanes.
· Push-back racking allows for high-density storage and supports LIFO inventory management, storing two to six pallets deep.
· Drive-in and drive-thru racking reduces the need for aisles. Drive-in is one-sided for LIFO, while drive-thru allows entry and exit on opposite sides, which is ideal for FIFO operations.
· Case and carton flow is similar to pallet flow but for cases and cartons. It’s often combined with push-back racking on upper levels for efficient FIFO case picking.
· Keg flow racking is specifically designed for beverage distributors and breweries to store and organize beer kegs.
Racking System Materials
Broadly speaking, there are two primary racking materials to choose from:
· Roll-formed racking is made of cold-rolled steel, shaped and processed at room temperature. This material suits warehouses with frequent layout changes, lighter products, and budget constraints.
· Structural racking is made from hot-rolled steel, giving it higher tensile strength and impact resistance. This makes structural racking better for warehouses with stable inventories, heavy pallets, frequent forklift interaction, and larger budgets.
Complement Your Racking System with the Right Forklifts
At Ring Power Lift Trucks, we understand the complexity of choosing a warehouse racking system. With over 60 years of experience, our commitment to quality and customer satisfaction is unparalleled. We have 19 locations throughout Florida, offering both new and used forklifts equipped with the latest technology, ensuring you find the perfect match for your racking system. For personalized forklift services across the Sunshine State, please contact us at 904-448-5438 today.
Comments