Warehouse Racking + in Florida
PALLET Racking systems & SHELVING for FLORIDA warehouses
Whether you're upgrading an existing warehouse or setting up a new logistics facility in Florida, our team is equipped to design and implement tailored pallet & cantilever racking, wire caging, shelving, mezzanines, modular in-plant office systems, and conveyor system solutions that meet your specific needs.
It's all about efficiencies and making the most of your warehouse space. Ring Power Lift Trucks understands your business needs for effective organization of warehouses, facility and inventory plays in streamlining operations.
We're here to help you with innovative warehouse racking or warehouse design services in Florida. Serving businesses in Lakeland, Tampa, Orlando, Jacksonville, Pompano Beach, Daytona Beach, Ocala, Tallahassee, and more. Click below or call us for a site review and estimate.
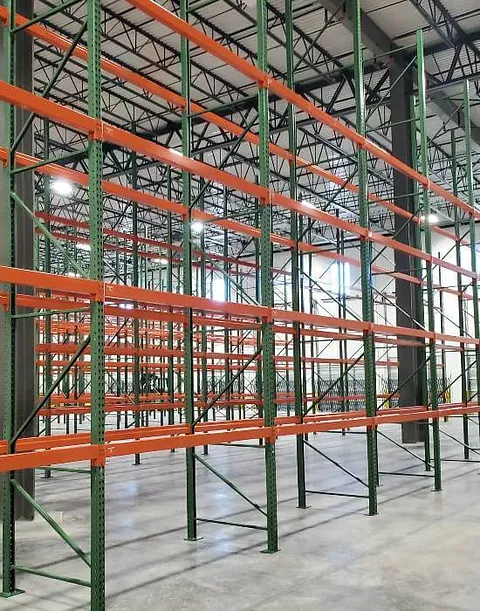
Types of Warehouse Pallet Racking
Pallet racking and warehouse storage systems refers to the system of organizing and storing goods within a warehouse or distribution center using specialized racks and shelves. These racks provide a structured framework to maximize the utilization of vertical space and facilitate efficient storage and retrieval of inventory.
- Roll-form cantilever racking options are ideal for storage of long, bulky products such as carpet rolls, lumber, pipe, tubing, etc.
- Structural cantilever racking is needed for storing irregular / awkwardly shaped items and is specially designed for easy front loading without obstruction. Call for a pallet racking estimate.
Read suggestions on selecting the right pallet racking system for your material handling operation.
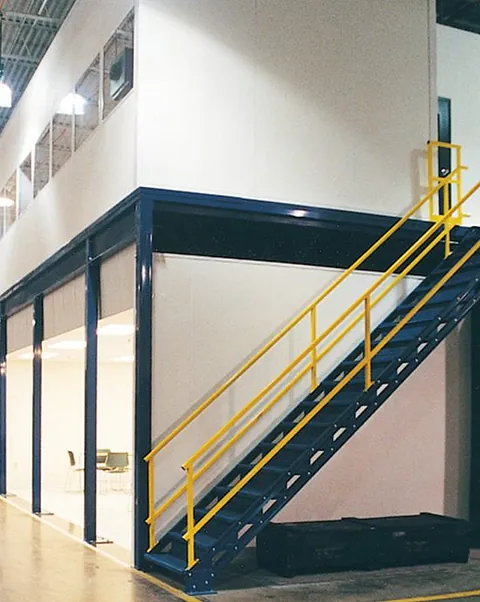
Modular
in-plant
Office Systems
When it comes to modular in-plant office systems we do it all. From the most basic economical 10'x10' prefab office to an environmentally controlled clean room or a two-story industrial complex. Ring Power Lift Trucks engineers a building inside and out and custom design a modular office system to fit your specific project needs. Call or complete the form for an modular office system quote.
Top Benefits of AN OPTIMIZED Warehouse
Optimizing a warehouse pallet racking system offers several key benefits contributing to improved warehouse efficiency and productivity. Here are some of the top advantages of utilizing warehouse racking systems:
- Increased Warehouse Storage Capacity – By utilizing the height of the warehouse effectively, businesses can store more inventory in a smaller footprint, freeing up valuable floor space for other operations.
- Enhanced Organization and Accessibility – With designated locations for each item, locating and retrieving goods becomes easier, reducing picking and replenishment time.
- Improved Inventory Control – With clear visibility of warehouse stock levels and easy access to items, businesses can monitor inventory accurately, track expiration dates, and implement effective inventory rotation strategies. This inventory control helps prevent stockouts, minimize waste, and optimize inventory turnover.
- Increased Operational Efficiency – By reducing the time spent searching for items and navigating through the warehouse, businesses can improve overall operational efficiency, increase order accuracy, and expedite customer deliveries.
- Safety and Risk Mitigation – Storing items on stable racks reduces the risk of damage or accidents caused by improper stacking or overcrowding.
- Scalability and Adaptability – Easily adjust, reconfigure, or expand racking to accommodate different product sizes, weights, or storage requirements. This scalability enables businesses to optimize their warehouse layout as their operations evolve.
- Cost Savings – By maximizing storage capacity, businesses can avoid the need for additional warehouse space or expensive off-site storage. The improved organization and accessibility of inventory reduce labor costs associated with picking and replenishment.
What to Know Before Purchasing & Installing Warehouse Racking
When purchasing and installing warehouse racking, several important factors should be considered to ensure the optimal design and functionality of the system. Here are some key considerations:
- Storage Requirements – Assess your specific storage needs, such as the types of goods, their dimensions, weight, and volume. Consider factors like pallet sizes, SKU variety, and specialized storage requirements.
- Warehouse Layout and Space – Analyze your warehouse layout and available space. Consider the dimensions, ceiling height, and any obstructions that may impact the racking installation.
- Inventory Accessibility and Flow – Plan for efficient inventory movement and accessibility. Consider the frequency of item retrieval and the picking methods employed.
- Racking System Type – Select the appropriate racking system type based on your storage requirements and operational needs.
- Safety Considerations – Prioritize safety features and standards when selecting a racking system. Ensure compliance with local safety regulations, and choose racks that are sturdy, durable, and capable of supporting the intended load capacity.
- Installation and Assembly – Determine whether you will handle the installation in-house or engage professional installation services. Ensure the racking installation is performed by experienced professionals who follow manufacturer guidelines and safety protocols.
- Future Expansion and Flexibility – Consider the potential for future growth and changes in your warehouse operations. Select a racking system that allows for scalability and easy reconfiguration.